فرآیند تولید شمش روی به روش الکترولیز
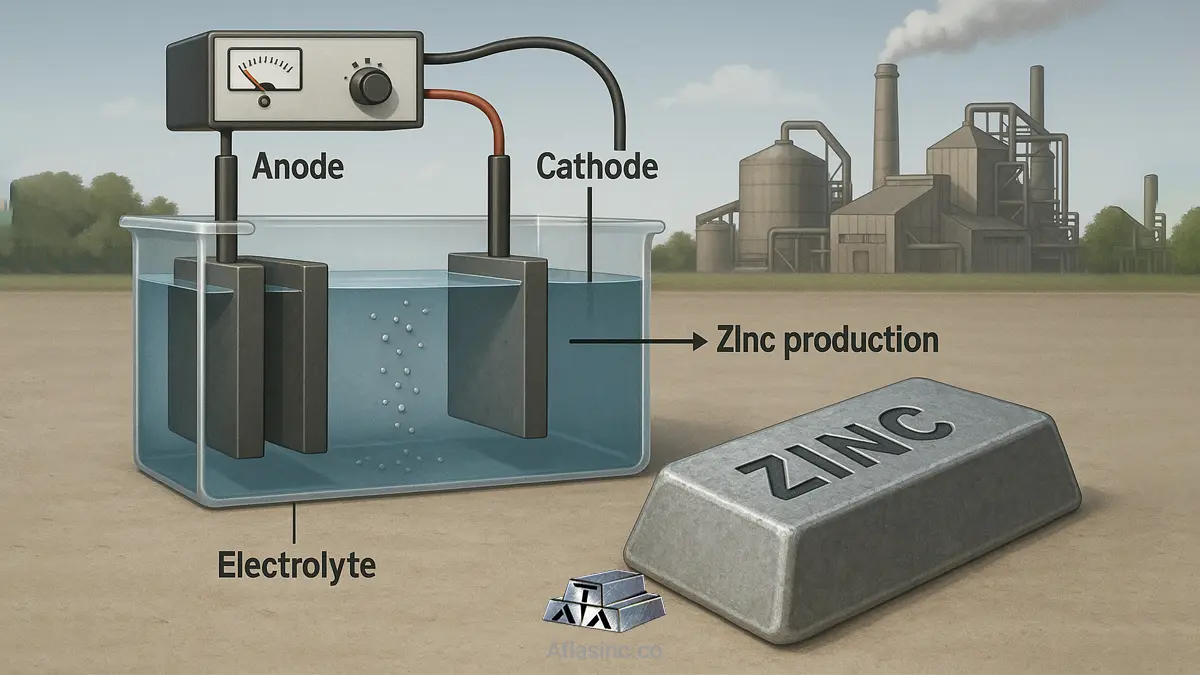
روی (Zinc) یکی از فلزات استراتژیک و پرکاربرد در صنایع مختلف است. این فلز با نماد شیمیایی Zn و عدد اتمی 30، دارای رنگ نقرهای مایل به آبی است و در دمای معمولی شکننده اما با افزایش دما، شکلپذیر میشود. مهمترین ویژگیهای فیزیکی آن شامل نقطه ذوب 419.5 درجه سلسیوس و چگالی 7.14 گرم بر سانتیمتر مکعب است.
از لحاظ اقتصادی، روی پس از آلومینیوم، مس و آهن، چهارمین فلز پرکاربرد جهان است. برخی از کاربردهای روی گالوانیزه کردن فولاد برای جلوگیری از خوردگی، آلیاژسازی (برنج، آلیاژهای آلومینیوم-روی) و صنایع باتریسازی، داروسازی و کودهای شیمیایی است.
مقایسه روشهای مختلف تولید روی
تولید صنعتی روی عمدتاً به دو روش حرارتی (پیرومتالورژی) و آبی (هیدرومتالورژی) انجام میگیرد. انتخاب روش مناسب به نوع سنگ معدن، میزان ناخالصیها، امکانات فنی و ملاحظات زیستمحیطی بستگی دارد. در ادامه به بررسی کامل هر دو روش و مقایسه آنها پرداخته میشود.
-
روشهای حرارتی (پیرومتالورژی) در تولید شمش روی
در این روش، کنسانتره سولفیدی روی (معمولاً اسفالریت) در دمای بالا به اکسید روی تبدیل میشود. سپس با استفاده از احیاگرهایی مانند کربن، فلز روی استخراج میگردد.
مراحل اصلی:
- تبدیل به اکسید روی (کلسیناسیون): کنسانتره ZnS در دمای 900-1000 درجه سانتیگراد با هوا واکنش داده و به ZnO تبدیل میشود.
- احیا: ZnO با کربن یا گاز مونوکسیدکربن در کورههای ویژه احیا شده و بخار روی تولید میشود.
- چگالش بخار روی: بخار روی در محفظههای سردتر به حالت جامد یا مایع تبدیل و جمعآوری میشود.
-
روشهای آبی تولید شمش روی (هیدرومتالورژی)
این روش به دلیل خلوص بالاتر محصول و سازگاری بیشتر با محیط زیست، در سالهای اخیر کاربرد بیشتری یافته است. در آن، کنسانتره ابتدا با اسید واکنش داده و سپس با الکترولیز به فلز روی تبدیل میشود.
مراحل اصلی:
- لیچینگ: کنسانتره روی با اسید سولفوریک واکنش داده و سولفات روی محلول تولید میشود.
- تصفیه محلول: حذف ناخالصیهایی مانند آهن، مس، کادمیوم و نیکل
- الکترولیز: بازیابی روی خالص از محلول سولفات روی
- ذوب و ریختهگری: تبدیل به شمش استاندارد
مقایسه اجمالی تولید شمش روی به روش الکترولیز
ویژگی | روش حرارتی | روش الکترولیز (آبی) |
دمای عملیاتی | بالا | پایین |
آلودگی محیطی | بالا | کمتر |
خلوص محصول | متوسط | بالا (بیش از 99.9%) |
مصرف انرژی | بیشتر | بهینهتر |
روش هیدرومتالورژی به دلیل راندمان انرژی بالاتر، خلوص بهتر و آلودگی زیستمحیطی کمتر، گزینهای مناسبتر برای صنایع مدرن تولید روی است، هرچند ممکن است سرمایهگذاری اولیه بیشتری نیاز داشته باشد
اصول علمی و تئوری فرآیند تولید شمش روی به روش الکترولیز
الکترولیز یکی از روشهای مهم در استخراج فلزات از محلولهای آبی است که نقش اساسی در تولید فلزات با خلوص بالا دارد. به بیان علمی تر الکترولیز یک فرآیندی الکتروشیمیایی است که در آن یونهای فلزی موجود در محلول، توسط جریان الکتریکی به شکل فلز آزاد بر روی کاتد رسوب میکنند. در فرآیند تولید روی، الکترولیز مرحله نهایی هیدرومتالورژی است که در آن یونهای Zn²⁺ از محلول جدا شده و به صورت فلز خالص روی سطح کاتد رسوب میکنند.
واکنش های اصلی | |
در محلول | ZnSO₄ → Zn²⁺ + SO₄²⁻ |
در کاتد (کاهش) | Zn²⁺ + 2e⁻ → Zn (فلز خالص) |
در آند (اکسایش آب) | H₂O → ½O₂ + 2H⁺ + 2e⁻ |
الکترودها: معمولاً از جنس آلومینیوم یا فولاد ضدزنگ (کاتد) و آند نامحلول (معمولاً تیتانیوم با پوشش خاص) هستند.
الکترولیت: محلول سولفات روی در اسید سولفوریک با غلظت مشخص.
منبع جریان: جریان مستقیم با شدت و ولتاژ کنترلشده.
این واکنشها در حضور جریان الکتریکی مستقیم و در دمای کنترلشده انجام میشوند
مواد اولیه و آمادهسازی شمش روی به روش الکترولیز
سنگ معدن اولیه مورد استفاده در تولید روی معمولاً از نوع سولفیدی است که غنیسازی آن برای افزایش بازده فرآیندهای بعدی ضروری است. اسفالریت (ZnS) رایجترین کانی روی است که پس از استخراج، فرآیندهای زیر را طی میکند:
- خردایش و آسیا: کاهش اندازه سنگ معدن با دستگاههای سنگشکن و آسیا
- فلوتاسیون: جداسازی ذرات سولفیدی باارزش به روش شناورسازی با استفاده از کفسازها و مواد شیمیایی مناسب
- تغلیظ: افزایش درصد روی در کنسانتره به حدود 50% یا بیشتر برای ارسال به واحد لیچینگ
فرآیند لیچینگ (استخراج به روش شیمیایی)
لیچینگ یکی از مراحل کلیدی در هیدرومتالورژی روی است که در آن کنسانتره سولفیدی با اسید سولفوریک واکنش داده و محلول حاوی ZnSO₄ حاصل میشود. خلوص این محلول اهمیت بالایی در فرآیندهای بعدی دارد
لیچینگ اسیدی: معمولاً در دمای 50-90 درجه سانتیگراد و pH پایین (زیر 2)
تصفیه محلول الکترولیت قبل از الکترولیز
قبل از الکترولیز، باید محلول سولفات روی از ناخالصیهایی که بر رسوبگذاری و کیفیت محصول تأثیر منفی میگذارند، پاکسازی شود. این تصفیه تضمینکننده عملکرد پایدار سلولهای الکترولیز است. آهن، مس، کادمیوم و نیکل ناخالصی های متداول در این محلول هستند که با روشهای شیمیایی نظیر افزایش pH، استفاده از عوامل کاهنده یا اکسیدکننده و تهنشینی حذف میشوند.
- آهن: اکسیداسیون Fe²⁺ به Fe³⁺ و تهنشینی به صورت هیدروکسید
- مس و کادمیوم: افزودن گرد روی برای تهنشینی آنها به صورت فلزی
- نیکل و کبالت: استفاده از روشهای جذب سطحی یا تبادل یونی
فرآیند الکترولیز در تولید شمش روی
فرآیند الکترولیز، مرحله نهایی در تولید روی است که در آن فلز روی از محلول الکترولیت رسوب داده شده و به صورت ورقهای خالص جمعآوری میشود. این مرحله به طراحی دقیق سلول و کنترل دقیق پارامترهای عملیاتی نیاز دارد.
-
طراحی سلولها
سلولها به صورت مخازن بزرگ از جنس PVC یا فولادی با آستر مقاوم در برابر اسید حاوی کاتدها و آندهای موازی ساخته میشوند. کاتدها معمولاً از جنس آلومینیوم یا فولاد ضدزنگ و آندها از تیتانیوم با پوشش فعال مقاوم به اکسیداسیون هستند.
-
پارامترهای عملیاتی
دمای محلول: 30-35 درجه سانتیگراد
چگالی جریان: 400-600 آمپر بر متر مربع
غلظت اسید H₂SO₄: 150-200 گرم بر لیتر
ولتاژ: حدود 2 ولت
-
تهنشینی روی
یونهای Zn²⁺ در حضور جریان مستقیم به کاتد منتقل شده و روی خالص رسوب میکند.
تهنشینی بهطور یکنواخت انجام میشود تا ورقهای فلزی با ضخامت یکنواخت تولید شوند
جمعآوری و ذوب شمش روی
پس از الکترولیز، لایههای روی از سطح کاتد جدا شده و مراحل ذوب و ریختهگری برای تولید شمش روی انجام میشود. استانداردسازی این شمشها بر اساس معیارهای بینالمللی صورت میگیرد. در این مرحله اقدامات زیر صورت می گیرد:
- جداسازی از کاتد: لایه روی به صورت مکانیکی یا حرارتی از ورق کاتد جدا میشود.
- ذوب: در کورههای ویژه (گازی یا القایی ) تا دمای 420-450 درجه سلسیوس ذوب میگردد.
- ریختهگری: فلز مذاب در قالبهای شمشریز ریخته شده و سرد میشود.
- استانداردسازی: تعیین گرید و شمارهگذاری شمشها بر اساس خلوص و ترکیب صورت می گیرد.
کنترل کیفیت و آنالیز محصول نهایی شمش روی
کنترل کیفیت از مراحل کلیدی در تضمین عملکرد نهایی محصول و پذیرش آن در بازارهای جهانی است. بررسی خلوص، خواص فیزیکی و شیمیایی از الزامات این مرحله است. مراحل کنترل کیفیت عبارتند از:
- آزمونهای شیمیایی: با استفاده از ICP یا AAS برای تعیین خلوص
- آزمونهای فیزیکی: بررسی چگالی، سختی، رنگ، شکل ظاهری
- استانداردهای بینالمللی: تطابق با استانداردهای ASTM B6، ISO 752
مزایا و معایب تولید شمش روی به روش الکترولیز
روش الکترولیز از منظرهای مختلفی چون خلوص محصول، مصرف انرژی، ملاحظات زیستمحیطی و پایداری اقتصادی بررسی میشود. در این بخش، مزایا و محدودیتهای آن با روشهای سنتی مقایسه میشود.
معیار | روش الکترولیز | روش حرارتی |
خلوص محصول | بسیار بالا | متوسط |
مصرف انرژی | کمتر | بیشتر |
آلودگی هوا | بسیار کم | بالا (انتشار SO₂) |
سرمایهگذاری اولیه | بالا | کمتر |
پیچیدگی تجهیزات | بیشتر | سادهتر |
روش الکترولیز با وجود نیاز به کنترل دقیق فرآیند و سرمایهگذاری بیشتر، به دلیل خروجی باکیفیت، پایداری زیستمحیطی و بهرهوری بالا، انتخابی مقرونبهصرفه و آیندهنگرانه در صنعت روی محسوب میشود
تکنولوژیها و تجهیزات مدرن در واحدهای تولید شمش روی به روش الکترولیز
پیشرفت فناوری نقش مؤثری در بهینهسازی فرآیندهای تولیدی از جمله تولید روی دارد. بهرهگیری از اتوماسیون، انرژیهای تجدیدپذیر و نانوفناوری به افزایش راندمان، کاهش هزینهها و کاهش اثرات زیستمحیطی منجر میشود.
- اتوماسیون
- کنترل دما، جریان و غلظت الکترولیت با سیستمهای PLC و SCADA
- کاهش نیاز به اپراتور انسانی و افزایش دقت
- انرژیهای نوین
- استفاده از برق خورشیدی و بادی در واحدهای الکترولیز
- بهکارگیری سیستمهای بازیافت انرژی از حرارت زاید
- فناوری نانو
- ساخت الکترودهایی با پوشش نانومتری برای کاهش مقاومت و افزایش سرعت تهنشینی
- افزایش پایداری تجهیزات و کاهش نیاز به تعویض مکرر
چالشها و ملاحظات زیستمحیطی تولید شمش روی به روش الکترولیز
با توجه به حجم بالای مصرف آب، مواد شیمیایی و تولید پساب در فرآیند تولید روی، رعایت اصول زیستمحیطی امری ضروری است. این چالشها در زمینه مدیریت پساب، بازیافت مواد و کاهش آلودگی بررسی میشود.
مدیریت پساب: تصفیه آبهای آلوده (حذف فلزات سنگین و اسید) با استفاده از رسوبدهی شیمیایی، فیلترها و روشهای بیولوژیکی
بازیافت مواد: استفاده مجدد از الکترولیت، بازیافت آندها، جمعآوری و بازیافت گرد روی و سایر مواد مصرفی
کاهش مصرف آب و انرژی: طراحی مدارهای بسته برای کاهش تلفات حرارتی و برقی و استفاده مجدد از الکترولیت
نتیجهگیری برای تولید شمش روی به روش الکترولیز
فرآیند الکترولیز به عنوان روش غالب و پیشرفته برای تولید شمش روی، با بهرهگیری از اصول علمی و تجهیزات مدرن، محصولی با خلوص بالا و اثرات زیستمحیطی کمتر ارائه میدهد. توجه به بهینهسازی مصرف انرژی، حذف ناخالصیها و مدیریت پسماند از الزامات حیاتی این صنعت است.
سوالات متداول تولید شمش روی به روش الکترولیز
-
آیا فرآیند الکترولیز در تولید شمش روی برای تمام معادن روی مناسب است؟
خیر، برای معادن روی که سنگ معدن با درصد خلوص پایین دارند یا ناخالصیهای مزاحم زیاد است، روشهای ترکیبی یا حرارتی ممکن است کارایی بیشتری داشته باشند.
-
خلوص نهایی شمش روی به روش الکترولیز چقدر است؟
بیش از 99.995 درصد، که از خلوص مورد نیاز در بسیاری از صنایع فراتر است.
-
آیا تولید شمش روی به روش الکترولیز هزینهبر است؟
در آغاز بله، اما در بلندمدت با مصرف انرژی کمتر و محصول باکیفیت، هزینهها جبران میشود.
-
چه فاکتورهایی در کیفیت نهایی شمش تاثیرگذارند؟
کیفیت الکترولیت، طراحی سلولها، کنترل دقیق دما و جریان، و خلوص مواد اولیه.
-
آیا امکان بازیافت مواد مصرفی در این فرآیند وجود دارد؟
بله، بسیاری از مواد مانند الکترولیتها، گرد روی، آندها و حتی پسابها قابلیت بازیافت دارند.