استخراج و تولید شمش روی
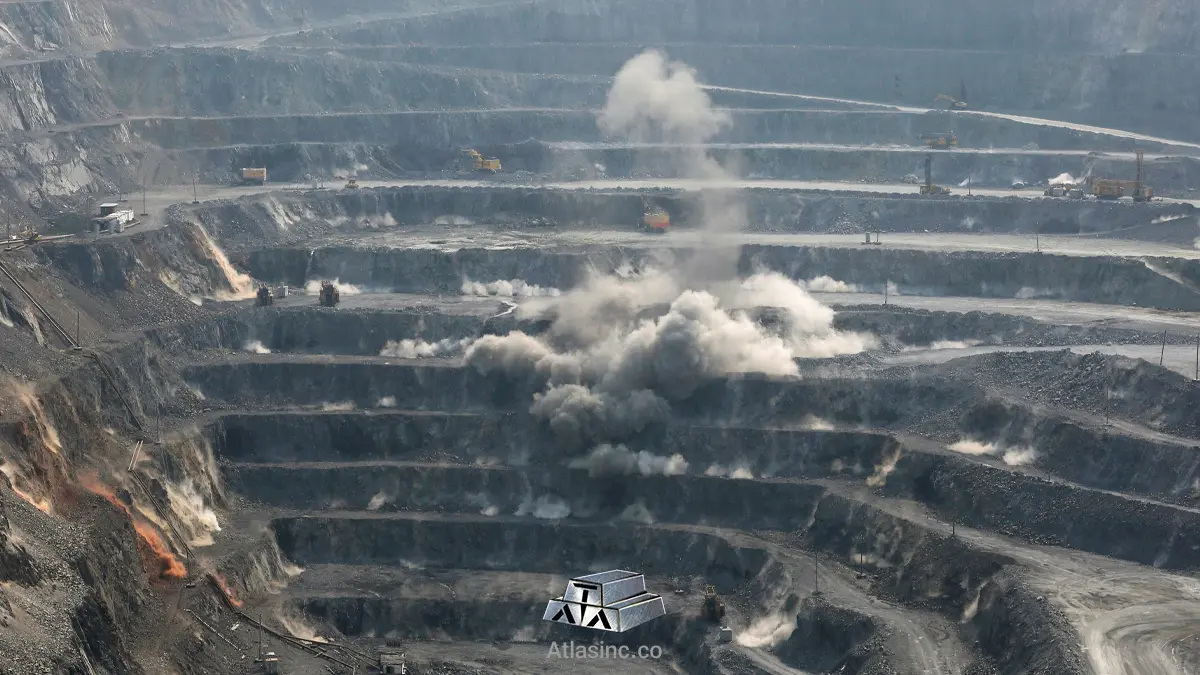
فلز روی یکی از مهمترین فلزات غیرآهنی است که در صنایع مختلفی همچون خودروسازی، برق و الکترونیک، و همچنین برای گالوانیزه کردن آهن و فولاد به کار میرود. فرآیند استخراج و تولید شمش روی از سنگ معدن روی (معمولاً از نوع سیگنایت یا کالامین) یک فرآیند پیچیده است که به روشهای مختلفی انجام میشود.
در این مقاله، مراحل استخراج و تولید شمش روی از قدیمیترین روشها تا جدیدترین تکنیکها بررسی خواهد شد. همچنین، ویژگیهای هر روش از نظر سختی، هزینه و خلوص شمش روی به تفصیل توضیح داده میشود. در نهایت، روشهای رایج در ایران و دلایل انتخاب آنها مورد بررسی قرار خواهد گرفت.
مراحل استخراج و تولید شمش روی
-
استخراج سنگ معدن روی
استخراج روی معمولاً از معادن باز یا معادن زیرزمینی انجام میشود. سنگهای معدن روی به دو صورت عمده یافت میشوند:
- کالامین (ZnCO₃): سنگ معدن غالب روی که شامل کربنات روی است.
- سینیت (ZnS): سنگ معدن دیگری که شامل سولفید روی است.
با استخراج این سنگها از معادن، ماده اولیه برای تولید شمش روی آماده میشود. شاید تمایل داشته باشید با تفاوت شمش روی با سایر فلزات غیر آهنی نیز آشنا شوید.
-
فرآوری سنگ معدن روی:
پس از استخراج سنگ معدن، باید فرآیندهای مختلفی برای جداسازی روی از سایر ناخالصیها انجام گیرد. فرآیندهای اصلی شامل موارد زیر است:
- فرآیند فلوتاسیون (Flotation): این فرآیند به ویژه برای سنگهای سولفیدی استفاده میشود. در این روش، سنگ معدن خرد شده در مخلوطی از آب و مواد شیمیایی خاص قرار میگیرد تا کانیهای روی از دیگر مواد جدا شوند
- فرآیند حرارتی (Roasting): در این روش، سنگ معدن سولفیدی در دمای بالا تحت تاثیر اکسیژن قرار میگیرد تا به اکسید روی تبدیل شود. این فرآیند همچنین برای تبدیل سولفیدها به اکسیدها کاربرد دارد.
- فرآیند شیمیایی (Leaching): در این مرحله، سنگ معدن به محلولهای شیمیایی مانند اسید سولفوریک یا اسید کلریدریک وارد میشود تا روی از دیگر مواد جدا شود. این روش بیشتر برای کانیهای کربناته استفاده میشود.
-
تولید شمش روی
پس از استخراج و فرآوری سنگ معدن، برای تولید شمش روی از مراحل ذوب و تصفیه استفاده میشود. در ادامه به برخی از روشها اشاره میشود:
روش تقطیری
یکی از قدیمیترین روشهای شناختهشده برای تولید شمش روی، روش تقطیری (Pyrometallurgical Distillation Process) بوده است. در این روش، سنگ معدن روی (عمدتاً اکسید روی یا سولفید روی پس از کلسینه شدن) در دمای بالا حرارت داده میشود و فلز روی از طریق تبخیر جدا شده و سپس در محیط سردتر متراکم میشود تا به شکل شمش روی درآید.
این روش نیاز به فناوری پیچیدهای ندارد و امکان استفاده از زغالسنگ بهعنوان سوخت وجود دارد و برای معادن کوچک و مناطقی که منابع الکتریکی محدود دارند مناسب است.
این روش معایبی نیز دارد از جمله اینکه:
- راندمان پایین و هدررفت بالای فلز روی در فرآیند تبخیر و تقطیر.
- خلوص نهایی شمش روی پایینتر از روشهای مدرن.
- مصرف انرژی بالا و انتشار زیاد گازهای آلاینده.
این روش در گذشته به دلیل سادگی و در دسترس بودن مواد اولیه رایج بود، اما امروزه به دلیل راندمان پایین و آلودگی محیطزیستی، در مقیاس صنعتی کمتر استفاده میشود.
روش الکترولیز (Electrowinning)
روش الکترولیز یکی از پیشرفتهترین و جدیدترین روشهای تولید شمش روی است که در آن از جریان الکتریکی برای استخراج فلز روی از محلولهای آبی استفاده میشود.
مراحل روش الکترولیز:
-
لیچینگ (Leaching)
ابتدا سنگ معدن روی (مانند کالامین یا سینیت) بهوسیله اسید سولفوریک یا سایر اسیدها حل میشود. این فرایند یونهای روی را در محلول آزاد میکند.
-
تصفیه محلول (Purification)
محلول حاصل از لیچینگ حاوی یونهای روی و ناخالصیهاست. از فرآیندهایی مانند رسوبدهی (precipitation) یا تبادل یونی (ion exchange) برای حذف ناخالصیها و تصفیه محلول استفاده میشود.
-
الکترولیز
محلول تصفیهشده به یک سلول الکترولیتی وارد میشود که در آن یونهای روی تحت تاثیر جریان برق قرار میگیرند و در کاتد رسوب میکنند. فلز روی در کاتد رسوب کرده و در نهایت به شمش روی تبدیل میشود.
مزایا | معایب |
خلوص بسیار بالا: روی تولیدی با روش الکترولیز میتواند تا 99.99% خلوص داشته باشد.
کمترین آلودگی: این روش باعث انتشار کمتر گازهای آلاینده مانند SO₂ و CO₂ میشود. بازیافت بالا: حتی سنگ معدنهای با عیار کم نیز میتوانند بهخوبی در این روش بازیافت شوند. |
هزینه سرمایهگذاری بالا: ساخت تأسیسات الکترولیز نیاز به سرمایهگذاری اولیه بالایی دارد.
نیاز به منابع انرژی: این روش به انرژی الکتریکی زیادی نیاز دارد که میتواند هزینهها را افزایش دهد.
|
روش کورهای (Pyrometallurgical) یا شعلهای
روش کورهای یکی از قدیمیترین و رایجترین روشها برای تولید شمش روی است که در آن از گرمای حاصل از سوختهای فسیلی برای ذوب و تصفیه سنگ معدن استفاده میشود.
مراحل روش کورهای:
-
تبدیل به اکسید
در ابتدا سنگ معدن روی (معمولاً سولفید روی) در کورههای با دمای بالا حرارت داده میشود تا به اکسید روی تبدیل شود. این مرحله بهنام کلسینیشن (calcination) شناخته میشود.
-
ذوب و تصفیه
اکسید روی با استفاده از دمای بسیار بالا ذوب شده و ناخالصیهای موجود در آن (مانند سیلیسیم، آهن و گوگرد) از بین میروند.
-
جداسازی فلز روی
در نهایت، روی از کوره خارج شده و به شکل شمش یا محصولات دیگر در میآید.
مزایا | معایب |
سرعت تولید بالا: این روش نسبت به روشهای دیگر سریعتر است.
هزینه پایین: هزینههای اولیه کمتری نسبت به روشهای الکترولیز دارد. مناسب برای سنگهای سولفیدی: این روش برای سنگهای سولفیدی که به راحتی در روشهای دیگر حل نمیشوند، مناسب است. |
خلوص پایینتر: شمش روی تولیدی دارای خلوص کمتری (حدود 90-98%) نسبت به روش الکترولیز است.
آلودگی محیطی: این روش به دلیل استفاده از سوختهای فسیلی و انتشار گازهای آلاینده مانند SO₂ و CO₂ آلودگی بیشتری تولید میکند. مصرف زیاد انرژی: نیاز به سوختهای فسیلی برای ایجاد دمای بالا باعث مصرف زیاد انرژی میشود. |
روش آلکالی (Alkaline Process)
روش آلکالی یا قلیایی برای استخراج روی از سنگهای کربناته یا برخی سنگهای سولفیدی استفاده میشود. در این روش، از محلولهای قلیایی برای حل کردن سنگ معدن و جداسازی روی استفاده میشود.
مراحل روش آلکالی:
-
انحلال سنگ معدن
سنگ معدن روی (معمولاً کالامین) در محلول قلیایی (مانند هیدروکسید سدیم) حل میشود. در این مرحله، یونهای روی از سنگ معدن جدا میشوند.
-
رسوبدهی
محلول حاصل از انحلال حاوی یونهای روی است که از آنها برای تولید سولفات روی یا سایر ترکیبات شیمیایی استفاده میشود. این ترکیبات سپس از محلول رسوب داده میشوند.
-
الکترولیز یا فرآیندهای حرارتی برای تولید شمش
در نهایت، یا از روش الکترولیز برای تولید شمش روی از محلول رسوبشده استفاده میشود یا از فرآیندهای حرارتی برای ذوب و تولید شمش روی استفاده میشود.
مزایا | معایب |
مناسب برای سنگهای کربناته: این روش بهویژه برای سنگهای کربناته مناسب است که در روشهای دیگر به سختی قابل استخراج هستند.
هزینه پایین: این روش به طور کلی هزینه کمتری نسبت به روشهای الکترولیز دارد. |
خلوص پایینتر: معمولاً در این روش، خلوص شمش روی کمتر از روش الکترولیز است.
آلودگی کمتر از کورهای: نسبت به روش کورهای، این روش آلودگی کمتری دارد، اما هنوز ممکن است گازهای سمی تولید کند. نیاز به تجهیزات خاص: نیاز به تجهیزات مقاوم در برابر محلولهای قلیایی و شرایط شیمیایی دارد. |
در جدول زیر سه روش ذکر شده در بالا از نظر سختی، هزینه و خلوص شمش روی مقایسه میشوند:
ویژگی | روش الکترولیز | روش کورهای (شعله ای) | روش آلکالی |
سختی فرآیند | دشوار، نیاز به تجهیزات دقیق و انرژی بالا | نسبتاً ساده و سریع | متوسط، نیاز به دقت در تنظیم شرایط شیمیایی |
هزینه | هزینه بالا (به دلیل مصرف انرژی و تجهیزات) | هزینه کم و اقتصادی | هزینه متوسط، به خصوص برای کانیهای عیار پایین |
خلوص | بسیار بالا (99.99%) | خلوص متوسط تا بالا (90-98%) | خلوص پایین تا متوسط |
سرعت تولید | کندتر به دلیل فرآیند الکترولیز | سریعتر و بهینهتر | متوسط، بستگی به نوع سنگ معدن |
در حال حاضر، روش کورهای (شعلهای) و روش الکترولیز از روشهای اصلی برای تولید شمش روی در سطح جهانی هستند.
روش کورهای به دلیل هزینه پایینتر و سرعت بالای تولید در بسیاری از کشورها (از جمله ایران) رایج است. این روش برای استخراج سنگهای سولفیدی که بیشتر در معادن ایران وجود دارند، مناسب است.
روش الکترولیز به دلیل خلوص بالا و کمتر بودن آلودگی محیطی، در کشورهای توسعهیافته و مناطقی که نیاز به تولید روی با خلوص بسیار بالا دارند (مانند صنایع الکترونیک و خودروسازی) استفاده میشود.
روش آلکالی کمتر مورد استفاده قرار میگیرد و معمولاً برای معادن خاص یا برای سنگهای خاص با عیار پایین مورد استفاده قرار میگیرد.
روشهای رایج تولید شمش روی در ایران
در ایران، روشهای کورهای و فرآیندهای شیمیایی (از جمله روشهای آلکالی) رایجتر از روشهای الکترولیز هستند. دلایل این انتخاب به شرح زیر است:
مناسب بودن برای منابع معدنی موجود: معادن روی ایران بیشتر سنگهای سولفیدی و کربناته دارند که فرآیندهای کورهای و شیمیایی برای آنها مناسبتر است.
هزینههای اقتصادی: روشهای کورهای با وجود اینکه خلوص کمتری تولید میکنند، اما هزینه کمتری دارند و از لحاظ اقتصادی به صرفهتر هستند.
دسترسی به فناوری: در حال حاضر، تکنولوژیهای پیشرفته الکترولیز هنوز در ایران کمتر در دسترس هستند و نیاز به سرمایهگذاریهای بالایی دارند.
نتیجهگیری
فرآیند تولید شمش روی با استفاده از روشهای مختلفی مانند الکترولیز، کورهای و آلکالی انجام میشود که هر کدام ویژگیها و مزایا و معایب خاص خود را دارند. در حال حاضر، روش کورهای به دلیل کم بودن هزینهها و سرعت بالا، در بسیاری از کشورهای جهان و همچنین ایران استفاده میشود. اگرچه روش الکترولیز دارای خلوص بالاتری است، اما به دلیل هزینههای بالا، هنوز در مقیاس صنعتی به طور گسترده در دسترس نیست. همچنین پیشنهاد می کنیم با کاربرد شمش روی در صنایع مختلف نیز آشنا شوید.
سوالات متداول تولید شمش روی
چه نوع سنگ معدن برای استخراج روی مناسب است؟
سنگهای سولفیدی (مثل سینیت) و کربناته (مثل کالامین) عمدتاً برای استخراج روی استفاده میشوند.
چه عواملی در انتخاب روش استخراج شمش روی تاثیرگذارند؟
نوع سنگ معدن، هزینهها، سرعت تولید و نیاز به خلوص شمش روی از عوامل اصلی تاثیرگذار در انتخاب روش استخراج هستند
آیا فرآیند الکترولیز برای تولید شمش روی در ایران به کار میرود؟
بله، اما این روش به دلیل هزینههای بالا و نیاز به تجهیزات خاص، کمتر در ایران رایج است و بیشتر از روش کوره شعلهای استفاده میشود.
آیا استفاده از روش کوره شعلهای به صرفهتر از الکترولیز است؟
بله، روش کوره شعلهای هزینه کمتری دارد و برای منابع معدنی موجود در ایران مناسبتر است.
چگونه میتوان خلوص شمش روی را افزایش داد؟
برای افزایش خلوص شمش روی، از روشهای الکترولیز استفاده میشود که به دلیل رسوب روی در کاتد، میتوان شمشهایی با خلوص بالا تولید کرد.