روشهای کاهش هزینه تولید روی
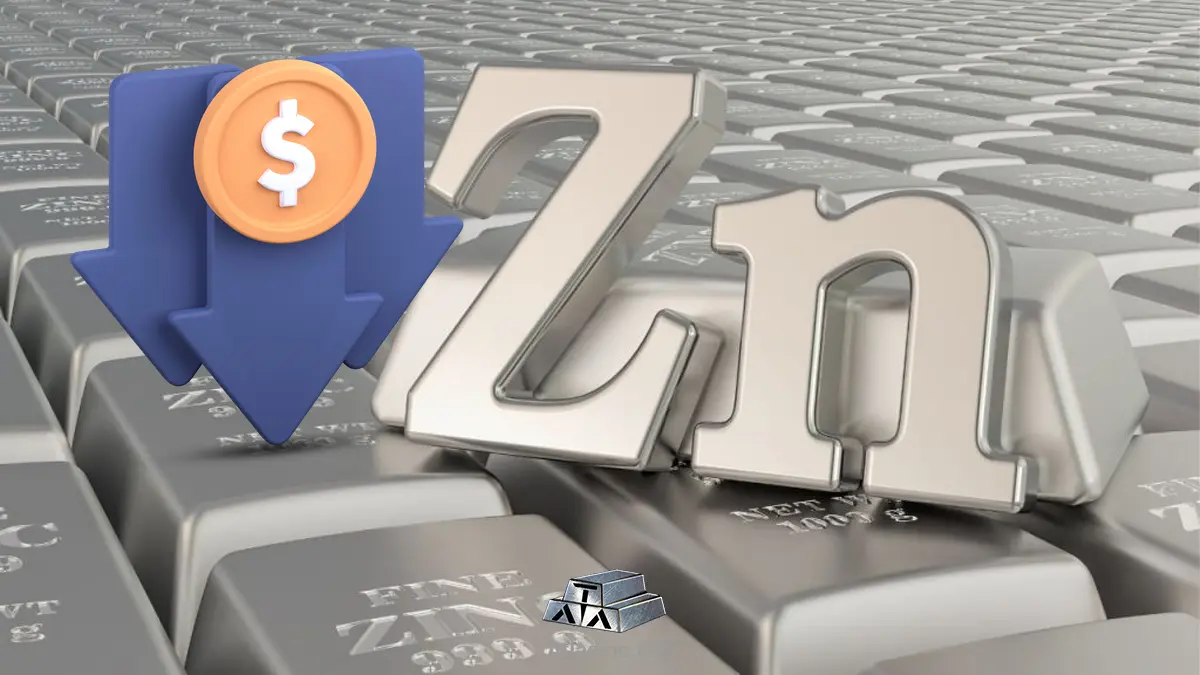
کاهش هزینه تولید روی نه تنها به افزایش بهرهوری و سودآوری شرکتها کمک میکند، بلکه نقش مهمی در بهبود کیفیت محصولات و پایداری محیط زیست ایفا میکند. هدف این مقاله ارائه راهکارهایی برای کاهش هزینه تولید شمش روی از طریق بهبود بهرهوری انرژی، استفاده از فناوریهای نوین و بهینهسازی فرآیندهای تولید است زیرا صنعت شمش روی از مهمترین صنایع مرتبط با فلزات محسوب میشود که در صنایع برق، الکترونیک و ساخت قطعات صنعتی کاربرد فراوان دارد. با توجه به تغییرات سریع بازارهای جهانی و افزایش رقابت، کاهش هزینه تولید روی به عنوان یکی از اولویتهای اصلی شرکتهای فعال در این حوزه مطرح میشود.
همچنین شاید تمایل به آشنایی با بهترین کارخانه های تولید شمش روی در ایران داشته باشید.
1-بررسی وضعیت فعلی تولید شمش روی
تولید شمش روی از مراحل متعددی مانند ذوب، پالایش، قالبگیری و سردسازی تشکیل شده است. هر یک از این مراحل میتواند نقطهای برای بروز هزینههای اضافی و اتلاف منابع باشد. از جمله عوامل موثر بر افزایش هزینه میتوان به موارد زیر اشاره کرد:
- مصرف انرژی بالا: فرآیند ذوب و پالایش نیازمند انرژی بالاست که هزینههای جاری را به شدت افزایش میدهد.
- ضایعات مواد اولیه: مدیریت ناکافی مواد اولیه و عدم کنترل دقیق بر فرآیندهای تولید میتواند باعث هدررفت قابل توجهی از مواد شود.
- نیروی انسانی و نگهداری تجهیزات: هزینههای مرتبط با نیروی کار متخصص و نگهداری تجهیزات صنعتی نیز از عوامل مهم افزایش هزینهها محسوب میشود.
با تحلیل دقیق وضعیت موجود و شناسایی نقاط ضعف، میتوان راهکارهایی برای کاهش هزینه تولید روی ارائه داد که در نهایت منجر به افزایش بهرهوری و بهبود کیفیت نهایی محصول میشود.
2-چگونه هزینه تولید روی را کاهش دهیم؟
در این بخش ابتدا به بررسی راهکارها و استراتژیهایی میپردازیم که میتوانند به طور مستقیم و غیرمستقیم موجب کاهش هزینههای تولید شوند. در این قسمت، با نگاهی جامع به فرایندهای موجود از مرحله ذوب تا قالبگیری، نقاط ضعف و گلوگاههای هزینهزا شناسایی میشوند. سپس با ارائه راهکارهای عملی مانند بهبود مدیریت مواد اولیه، اتوماسیون فرآیندها، استفاده از فناوریهای نوین و بهینهسازی مصرف انرژی، مسیرهایی مشخص برای کاهش هزینهها ترسیم میشود. هدف از این بخش، فراهم آوردن یک چارچوب عملی و استراتژیک است تا مدیران و کارشناسان صنعت شمش روی بتوانند با اتخاذ تصمیمات مستدل و مبتنی بر داده، به افزایش بهرهوری و کاهش هزینههای تولید دست یابند.
2-1-بهینهسازی مصرف انرژی در ذوب روی
فاز ذوب در تولید شمش روی به دلیل مصرف انرژی بسیار بالا، یکی از بخشهای حساس از نظر هزینه است. بهینهسازی فرآیند ذوب از طریق استفاده از سیستمهای پیشرفته کنترل حرارتی و بازیابی حرارت میتواند تاثیر چشمگیری بر کاهش مصرف انرژی داشته باشد. استفاده از تکنولوژیهای نوین مانند کورههای پرفشار و سیستمهای اتوماسیون هوشمند، نه تنها به بهبود کیفیت ذوب کمک میکند بلکه موجب کاهش هزینههای عملیاتی نیز میشود.
از جمله راهکارهای عملی برای بهینه سازی مصرف انرژی میتوان به موارد زیر اشاره کرد:
- سیستمهای نظارت و کنترل هوشمند: نصب حسگرها و سیستمهای نظارتی جهت ثبت لحظهای دما و جریان حرارتی به شناسایی نقاط اتلاف انرژی کمک کرده و امکان تنظیم بهینه فرآیند را فراهم میآورد.
- بهینهسازی زمانبندی عملیات: برنامهریزی دقیق برای کاهش زمانهای بیکاری تجهیزات و بهینهسازی سیکلهای تولید از جمله اقدامات مؤثر در کاهش هزینه انرژی است.
اجرای این راهکارها منجر به کاهش قابل توجه هزینههای انرژی و در نتیجه کاهش هزینه تولید روی خواهد شد که در بلندمدت موجب افزایش سودآوری و پایداری اقتصادی شرکتها میشود.
2-2-مدیریت مواد اولیه و کاهش ضایعات
یکی از مهمترین عوامل موثر در کاهش هزینه تولید روی، بهینهسازی استفاده از مواد اولیه است. مدیریت مواد اولیه از طریق کاهش ضایعات و مدیریت دقیق موجودی مواد میسر است که در ادامه به توضیح این راهکارها میپردازیم:
- انتخاب منابع با کیفیت: استفاده از مواد اولیه با استانداردهای بالا و کنترل دقیق کیفیت ورودیها موجب کاهش ضایعات ناشی از کیفیت پایین میشود.
- کنترل دقیق ذخیرهسازی: پیادهسازی سیستمهای انبارداری هوشمند که میزان مصرف و باقیمانده مواد اولیه را نظارت کنند، از اتلاف مواد جلوگیری میکند.
- بازیافت و استفاده مجدد از ضایعات: تدوین فرآیندهایی برای بازیافت ضایعات روی تولیدی و بازگرداندن آنها به چرخه تولید، هزینههای مربوط به مواد اولیه را به طور چشمگیری کاهش میدهد.
با بهبود مدیریت مواد اولیه و کاهش ضایعات، میتوان هزینههای تولید را کاهش داده و در عین حال از منابع طبیعی به صورت بهینهتری بهره برد.
2-3-اتوماسیون و بهینهسازی فرآیندهای تولید
اتوماسیون در فرآیندهای تولید یکی از موثرترین راهکارها برای کاهش هزینههاست. استفاده از سیستمهای اتوماسیون باعث کاهش خطاهای انسانی، افزایش دقت و سرعت عملیات و بهبود کیفیت محصولات میشود.
راهکارهای اجرایی برای این مورد عبارتند از:
- یکپارچهسازی سیستمهای کنترلی: استفاده از نرمافزارهای پیشرفته و سیستمهای نظارت مرکزی برای هماهنگی بهتر میان مراحل مختلف تولید.
- استفاده از رباتیک: به کارگیری رباتهای صنعتی در بخشهای حمل و نقل مواد، بستهبندی و کنترل دقیق فرآیندها.
- پیادهسازی خطوط تولید خودکار: طراحی خطوط تولید خودکار که بتوانند با حداقل مداخله انسانی عملیات تولید را به صورت بهینه انجام دهند.
با وجود هزینههای اولیه پیادهسازی اتوماسیون، سرمایهگذاری در این فناوریها در بلندمدت موجب کاهش هزینههای عملیاتی، بهبود بهرهوری و افزایش کیفیت نهایی محصول خواهد شد.
2-4-نقش فناوریهای نوین در کاهش هزینهها
فناوریهای نوین مانند اینترنت اشیاء (IoT)، هوش مصنوعی (AI) و دیجیتالسازی فرآیندها، به عنوان ابزارهای قدرتمندی در جهت کاهش هزینه تولید روی شناخته میشوند.
- اینترنت اشیاء (IoT): استفاده از حسگرهای هوشمند برای جمعآوری دادههای دقیق در زمان واقعی و نظارت بر عملکرد تجهیزات صنعتی.
- هوش مصنوعی (AI): تحلیل دادههای حاصل از فرآیندهای تولید جهت پیشبینی خرابیها، نگهداری پیشگیرانه و بهینهسازی زمانبندی تولید.
- دیجیتالسازی: پیادهسازی سیستمهای مدیریت دیجیتال جهت کنترل فرآیندها و کاهش خطاهای انسانی.
فناوریهای نوین باعث افزایش بهرهوری، کاهش ضایعات و بهبود کیفیت محصولات میشوند. استفاده از این فناوریها نه تنها هزینههای تولید را کاهش میدهد بلکه موجب ارتقای سطح رقابت شرکتها در بازار میشود.
3-تحلیل هزینه و بهرهوری در تولید روی
برای دستیابی به کاهش هزینه تولید روی، بررسی دقیق هزینههای سرمایهگذاری، هزینههای عملیاتی و محاسبه بازگشت سرمایه (ROI) ضروری است. استفاده از مدلهای تحلیل هزینه-فایده میتواند به تصمیمگیریهای بهینه کمک کند.
در فرآیند تحلیل هزینه و بهرهوری در تولید روی، تعیین و استفاده از شاخصهای کلیدی عملکرد (KPIs) به عنوان ابزاری حیاتی برای سنجش و پایش عملکرد عملیاتی مطرح است. این شاخصها به مدیران و متخصصان این امکان را میدهند تا بهطور دقیق، نقاط قوت و ضعف فرآیندهای تولید را شناسایی کرده و با استفاده از دادههای واقعی، تصمیمات بهینهسازی را اتخاذ کنند. از طریق اندازهگیری عوامل مهمی مانند مصرف انرژی، میزان ضایعات مواد اولیه، بهرهوری تولید و کیفیت محصول، میتوان به صورت سیستماتیک روند بهبود عملکرد را دنبال و تاثیر اقدامات کاهش هزینه را به وضوح ارزیابی نمود. این رویکرد نه تنها به کاهش هزینههای عملیاتی منجر میشود بلکه به افزایش رقابتپذیری و پایداری در بازار نیز کمک میکند.
- کاهش مصرف انرژی: درصد کاهش هزینههای انرژی پس از بهینهسازی فرآیند ذوب.
- کاهش ضایعات مواد اولیه: بهبود درصد استفاده بهینه از مواد اولیه و کاهش ضایعات.
- افزایش بهرهوری تولید: افزایش تعداد واحدهای تولید شده در واحد زمان.
- بهبود کیفیت محصول: کاهش نرخ خطاها و افزایش رضایت مشتریان.
با جمعآوری دادههای مربوط به وضعیت تولید قبل و بعد از اجرای راهکارهای پیشنهادی، میتوان تاثیر این اقدامات را از نظر اقتصادی و بهرهوری ارزیابی نمود. مطالعات موردی و گزارشهای صنعتی نمونههای موفق را نشان میدهند که اجرای این راهکارها منجر به کاهش چشمگیر هزینههای تولید شده است.
4-نتیجهگیری برای کاهش هزینه تولید روی
در این مقاله به بررسی جامع راهکارهای کاهش هزینه تولید روی پرداخته شد. از طریق تحلیل وضعیت فعلی تولید شمش روی، ارائه راهکارهای بهینهسازی مصرف انرژی در ذوب، مدیریت مواد اولیه و کاهش ضایعات، اتوماسیون فرآیندها، استفاده از فناوریهای نوین و تحلیل دقیق هزینه و بهرهوری، میتوان به افزایش بهرهوری و کاهش هزینههای تولید دست یافت. اجرای این راهکارها نه تنها موجب بهبود عملکرد شرکتها میشود بلکه در بازار رقابتی جهانی مزیت رقابتی قابل توجهی ایجاد میکند. مدیران و متخصصان صنعت شمش روی میتوانند با بهرهگیری از این استراتژیها، به سوی تولیدی پایدارتر و اقتصادیتر حرکت نمایند.
5-سوالات متداول در راستای کاهش هزینه تولید روی
چرا کاهش هزینه تولید روی اهمیت دارد؟
کاهش هزینهها موجب افزایش بهرهوری، سودآوری و رقابتپذیری شرکتها میشود و از مصرف بیرویه انرژی و منابع جلوگیری میکند.
چه اقداماتی برای بهینهسازی مصرف انرژی در ذوب روی پیشنهاد میشود؟
استفاده از کورههای پیشرفته، نصب سیستمهای نظارتی هوشمند و بهینهسازی زمانبندی عملیات از جمله راهکارهای کلیدی هستند.
چگونه میتوان مدیریت مواد اولیه را بهبود داد؟
انتخاب مواد اولیه با کیفیت، کنترل دقیق ذخیرهسازی و اجرای فرآیندهای بازیافت ضایعات از روشهای موثر در مدیریت بهینه مواد اولیه است.
اتوماسیون چه نقش مهمی در کاهش هزینهها دارد؟
اتوماسیون موجب کاهش خطاهای انسانی، بهبود هماهنگی فرآیندها و افزایش سرعت تولید میشود که در بلندمدت به کاهش هزینههای عملیاتی منجر میگردد.
فناوریهای نوین چگونه به کاهش هزینه تولید روی کمک میکنند؟
استفاده از اینترنت اشیاء (IoT)، هوش مصنوعی (AI) و دیجیتالسازی فرآیندها به بهبود نظارت، پیشبینی خرابی و بهینهسازی منابع کمک میکند که در نهایت هزینههای تولید کاهش مییابد.
چگونه میتوان تأثیر این راهکارها را از نظر اقتصادی ارزیابی کرد؟
با استفاده از مدلهای تحلیل هزینه-فایده، شاخصهای کلیدی عملکرد و مقایسه دادههای قبل و بعد از اجرای راهکارها میتوان بازگشت سرمایه و افزایش بهرهوری را سنجید.